
Machine tool automation - The right planning
Topic video
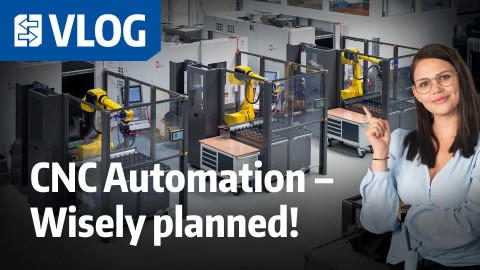
This video is hosted on YouTube. To watch the video please accept the media cookies in the privacy settings.
Machine tool automation: Spoiled for choice
Automated loading and unloading of machine tools, such as CNC milling machines, is now a standard feature in many places in the machining industry. The reason for this is that increasing cost and competitive pressure requires optimization of in-house processes, including the efficient use of available resources.
For companies without automation or with a low level of automation, the first steps towards automating their production are therefore decisive in setting the course. For them, it is important to clarify which solution - within the enormously diverse automation systems - is an optimal entry solution.
Whether part handling, pallet automation, linear-guided or in the form of industrial robot automation, automation technology providers usually have their own philosophy on how to handle machine loading and what options are offered for storage.
Companies that want to automate a CNC machine need an actual state analysis. To make it easier for you to find answers to the relevant questions, we have summarized the most important parameters on machine tool automation for you here.
Actual state analysis: how to get started the right way
With the help of an actual state analysis, you as a machining company bring transparency to your own process and set the course for the future automation solution. For milling machines, the following aspects should be included in the consideration:
Own product
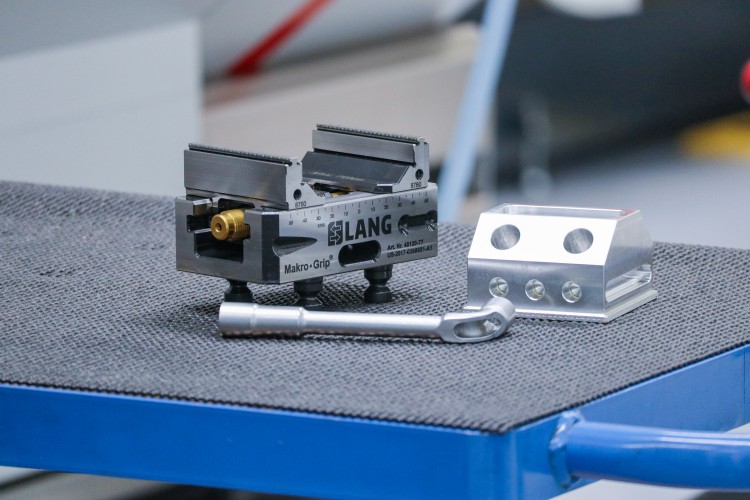
In the first step, deal with your own range of parts and their production:
- What types and sizes of components do I produce?
- What percentage of the parts spectrum can be covered by an automation system?
- What are the cycle times?
- Which batch sizes are produced?
The sum of workpieces to be processed and the production time is the basis for decisions such as
- Does machine tool automation manage to efficiently fill free machine capacities during evening and night hours?
- Does this open up time windows during the day that machine operators can invest in other tasks?
- Do the shapes of the components directly affect the way they are clamped or gripped?
These key points can be used to determine a rough direction of automation.
Type and age of the machine tool
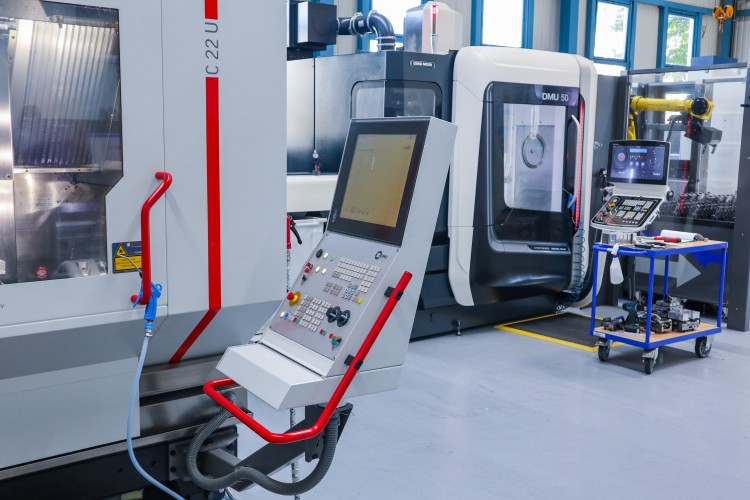
New purchase for more output? Or would it be better to increase efficiency by retrofitting an existing system? This decision has to be made first, taking into account the age and type of the existing CNC machines. The fact is: Depending on the year of construction or manufacturer, automation can be easier or much more difficult to implement. In addition, there is the clarification of how much the existing milling machine must be modified in order to be able to technically connect an automation system:
- Which interfaces are already there?
- How should the loading take place? Through an automated machine door or better through a side window? And: Do they already exist or are structural adjustments to the machine necessary?
- What are the specifics inside the machine?
- How easy or difficult is it to implement the zero point clamping system, which is essential for automated manufacturing?
- How shall it be operated? Does this require a media interface that has to be retrofitted separately?
In sum, each individual point must be carefully weighed up in terms of meaningfulness, costs and benefits, but also opportunities and risks..
Infrastructure within a machine shop
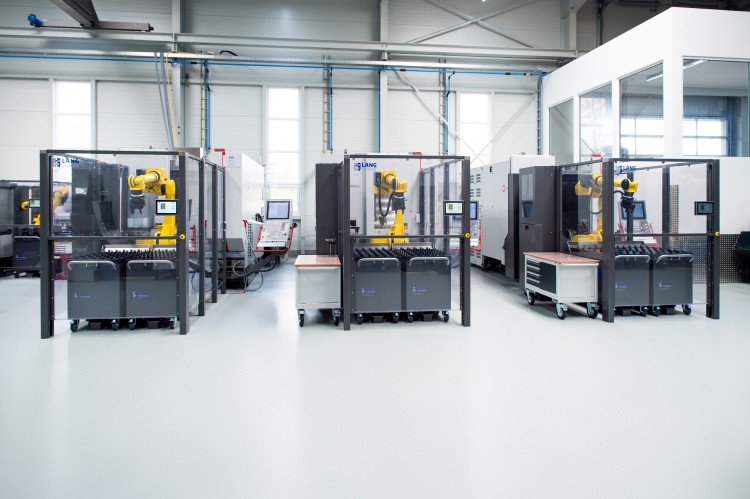
Automation changes almost everything - first and foremost its own production environment: Machine tool automations result in "new" processes, which in turn influence the spatial design and logistics within a production facility.
This "big picture" must not be lost sight of. Also of great importance: How much spatial capacity do I have at all for machine tool automation? Is the available space sufficient to connect the automation of a milling machine? Do I place the workpiece storage in front of or next to the CNC machine?
Own staff and complexity of the automation
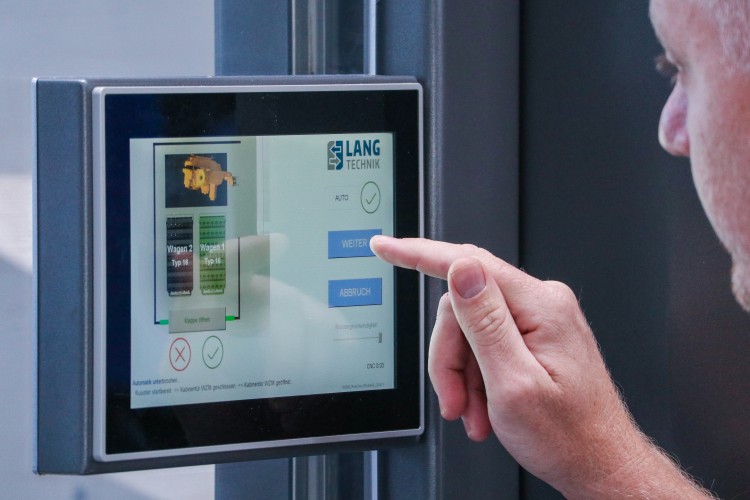
The question of the complexity of an automation system also has a direct influence on personnel issues:
- Do I have enough qualified personnel available?
- Is the automation designed so simply that even unskilled / semi-skilled personnel can be trained and have a handle on the operation of the automated CNC milling machine?
- What is the impact on automation if the number of skilled workers is large?
- Taking the above issues into account, does a simple automation solution with intuitive operation make more sense or is the investment in a complex system "worth it"?
Independence from the machine manufacturer / type
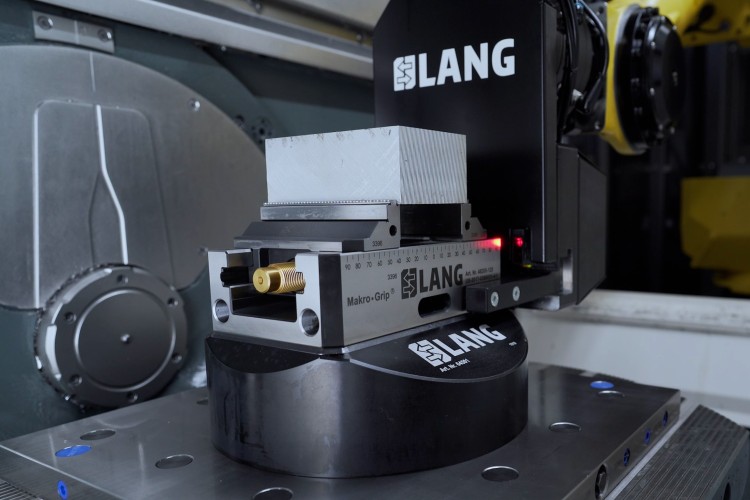
New purchase or retrofit? This question is also relevant when looking at the machinery. Here, the question almost always arises as to how much you want to tie yourself to a particular manufacturer. Independence - self-sufficiency in terms of machine type and manufacturer - can be an advantage. If a machine tool has to be replaced due to a defect or age, a company remains flexible in the selection of a successor CNC machine.
Here, topics such as communication and interfaces and legal issues are then on the agenda. Without detailed information, it is not possible to validate a statement for or against a new acquisition or retrofit. All general conditions must always be considered before such a decision is made.
Many years of experience in automation
LANG Technik was the first workholding manufacturer to start in the business field of automation more than 15 years ago. (More about the company history on the About LANG page) Using automation solutions, the aim was to optimize the company's own production processes and to fight the increasing cost pressure. For good reason: Relocating production abroad was and is not an option for LANG Technik.
Automation quickly had a positive effect: the company grew. Whereas the machine tools were previously loaded and unloaded manually by the machine operators, this has now been done by means of an integrated automation system. As a result, not only the output increased. The machine operators were able to use the resulting time windows for other activities - the working day became more variable.
By working with the machine tool automations on a daily basis, those responsible put the applications through their paces and ensured continuous (further) development of practical automation solutions.
More productive through automated manufacturing
Nowadays automated production processes are standard at LANG Technik with a rate of 95%. (See also press report: Investment in the future). LANG works in single-shift operation. Unmanned production in the evening and night hours allows better utilization of machine capacities and generates a higher spindle running time without additional personnel. Another plus: nighttime electricity is cheaper. The gain in machine hours through machine tool automation not only increases output, but also eliminates the often relatively unproductive late or night shifts.
Entire series can be machined with the help of an automated CNC machine, at least in the first OP - with the right workholding system, often even completely in one OP. Time-critical jobs can be executed more flexibly and more easily.
Last but not least, the satisfied customer is grateful for the shortening of production and delivery times.
The lower machine hourly rate and increased productivity make parts less expensive while maintaining the same quality. The cost advantage achieved in combination with consistently high quality standards pays into the competitiveness of such companies.
Does an automation solution pay off for your company?
We are quite sure! Find out for yourself with our payback calculator.
Payback calculator