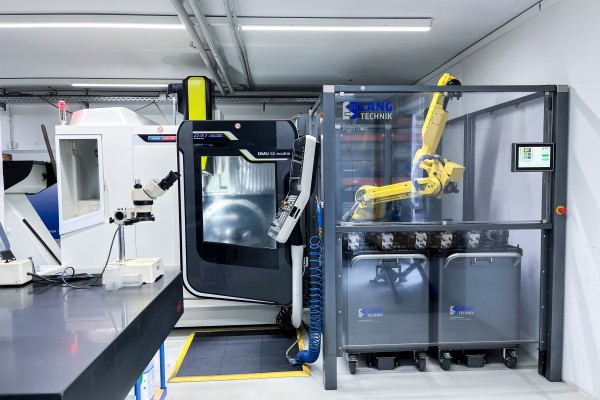
Compact solution with a big impact - Flexible automation on a small footprint
Topic video
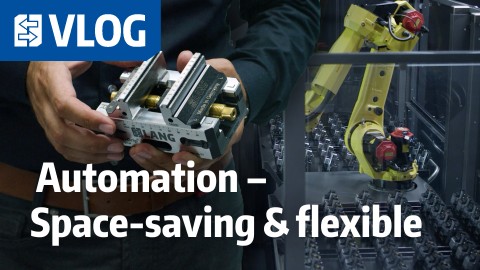
This video is hosted on YouTube. To watch the video please accept the media cookies in the privacy settings.
Space requirements vs. available space
It has now been proven thousands of times: Automation systems increase the productivity of a production line. With their help, machines continue to produce into the night - often without the involvement of a human operator. During the day, they create completely new possibilities and offer capacities. The big issue is that automation systems are often real space consumers and take up valuable production area. The desire for more output via a cleverly designed automation system is usually torpedoed by limited space - a real dilemma. (You can read about the other factors that need to be taken into account in Machine tool automation - the right planning).
However, this is not a dilemma that cannot be solved, because we at LANG Technik were already confronted with this issue after the turn of the millennium: Again and again, we had to increase our output in production due to increased demand for workholding systems. We reached our limits - new milling machines were often not an option for reasons of space. So we increased the capacity utilization of the existing machines. Here, too, there were hurdles to overcome, because the prevailing shortage of skilled workers made it difficult to increase personnel and thus also to run multiple shifts.
Not to mention the quality, because it was clear: What leaves the warehouses of LANG Technik must be consistently excellent, whether produced during the day or at night. We went in search of solutions to provide the machines with automated input and to relieve our workforce where possible.
Yes, it's true: Many automation concepts taking up an enormous amount of space. But not all of them, as our HAUBEX proves. The storage system for vises and workpieces in the tool magazine impressively proves that there are sometimes creative solutions that fit even into the smallest production, or can even be integrated into the milling machine. What we are particularly pleased about is that the connection of the system is not complicated - not always a matter of course with automation systems.
How did we achieve this? We focused on one question: How compact can such multi-variant solutions be built and where does the customer have the most options and as many clamping devices as possible on the smallest footprint?
From the Eco-Tower to RoboTrex: the ultimate edge in automation
This is not new territory for us: For a long time, the Eco-Tower was the state of the art in LANG Technik's automation range. With its "spiral tower", which made ideal use of the hall height and the possibility of storing 60 clamping devices, it was a popular aid for customers worldwide for a long time. For many years, the Eco-Tower shaped the look of machine shops and created growth potential by increasing output.
But stagnation is not our thing: We test and build, dismiss what is not practical and start with new ideas. The trend towards using industrial robots in manufacturing in particular proved to be very promising. Here we focused on the development of new ideas for the storage of clamping devices.
The result was RoboTrex. In a nutshell: even more storage capacity and that with an increase in flexibility. RoboTrex combines modern industrial robot technologies with almost intuitive operation. In terms of communication with the machine tool, RoboTrex makes it easy for customers. And when it comes to workpiece and clamping device storage, the ingeniously simple as well as flexible solution of mobile storage trolleys on which the vises are stored prevailed.
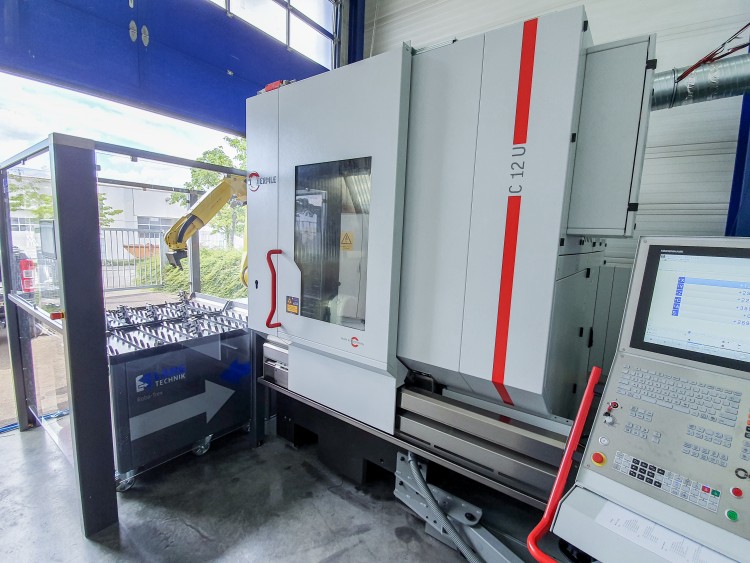
Speaking of intuitive operation, we at LANG Technik are convinced that a sound automation system is really good when it can be quickly understood and operated by as many workers as possible - even unskilled ones. The already pre-programmed system, a clear display and the full access to the complete memory make it possible.
The opportunities in application are wide-ranging: RoboTrex facilitates batch production of identical workpieces, but also processes wider or taller workpieces and reliably manufactures individual parts. Customers can therefore look forward to covering the majority of their component spectrum in automated, unmanned production with RoboTrex.
But that's not all: the 84 5-Axis Vises can be stored on 3.5 m² of floor space. This makes RoboTrex an automation system for even the smallest workshop, which scores with all its advantages. By the way: The storage capacity can be doubled by adding two more automation trolleys. This puts RoboTrex among the best automation systems, especially when the machine shop is crowded.

Does an automation solution pay off for your company?
We are quite sure! Find out for yourself with our payback calculator.
Payback calculator